Automated Welding with Cobots: Revolutionizing Fabrication for SMEs
In the fast-evolving world of manufacturing and fabrication, Small and Medium-sized Enterprises (SMEs) face constant pressure to remain competitive while navigating challenges such as skilled labour shortages, rising production costs, and increasing demand for customization. Among the many technological advancements reshaping the industry, collaborative robot (cobot) welding has emerged as a game-changer. Unlike traditional industrial robots, cobots are designed to work alongside human operators, combining precision automation with human ingenuity. For fabrication SMEs, cobot welding represents a transformative tool that improves efficiency, lowers costs, and enhances operational flexibility.
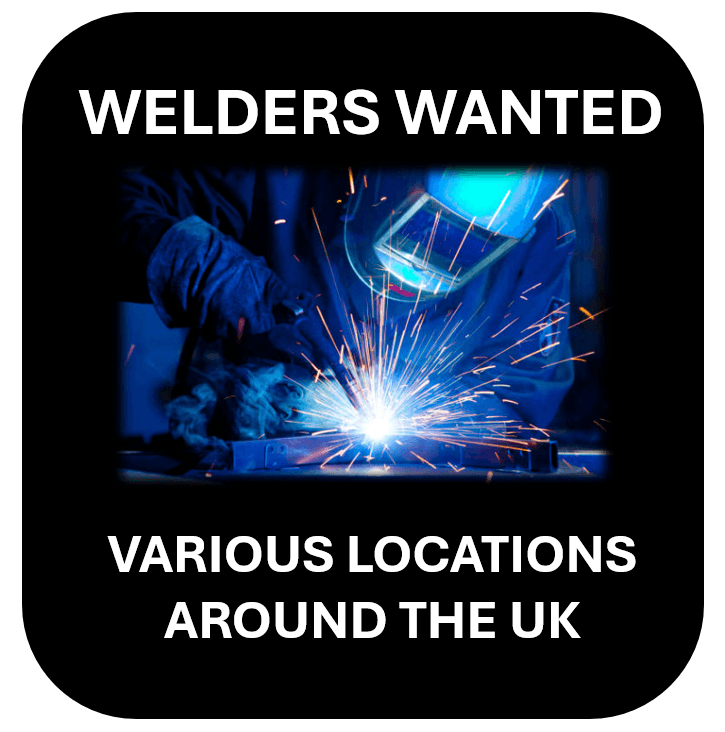
Addressing Labour Shortages
One of the most significant challenges faced by SMEs in the fabrication sector is a shortage of skilled welders. Welding is a demanding profession that requires precision, experience, and adaptability to diverse projects. However, the aging workforce and declining interest among younger generations in manual trades have led to a labour gap. Cobot welding offers a practical solution.
Cobots are designed to execute repetitive and precision-demanding automated welding tasks with minimal input and supervision. This allows companies to allocate their skilled welders to more complex or custom projects while cobots handle routine or high-volume tasks. Moreover, cobots are easy to program, enabling operators with minimal robotics experience to set them up and oversee their operation. This democratization of technology reduces the reliance on specialized labour, which can be difficult and expensive to source.
Enhancing Productivity and Efficiency
Efficiency is a cornerstone of competitive advantage in fabrication. Traditional welding processes, particularly when performed manually, can be time-consuming and inconsistent due to human fatigue and variability. Cobots excel at mitigating these inefficiencies.
Equipped with advanced sensors and precise programming, cobots deliver consistent weld quality across long production runs. This precision reduces material waste and minimizes the need for rework, leading to faster turnaround times. Additionally, cobots can operate continuously with minimal breaks, enabling SMEs to meet tight production deadlines and scale operations to accommodate larger contracts.
For example, a fabrication SME producing components for the automotive or aerospace industries can use cobots to ensure adherence to stringent quality standards while maintaining high production rates. By reducing lead times and improving reliability, SMEs can attract and retain clients in competitive markets.
Cost Savings and Accessibility
Historically, industrial automation was perceived as a luxury accessible only to large manufacturers with substantial capital investments. Traditional industrial robots require significant upfront costs, extensive programming, and dedicated safety infrastructure. Cobots, on the other hand, offer a more accessible alternative for SMEs.
Cobots are generally more affordable than traditional robots and boast shorter implementation timelines. They can be integrated into existing production lines with minimal disruption and without the need for expensive and ridged safety enclosures.
Furthermore, many cobot manufacturers offer flexible leasing or financing options, reducing the barrier to entry for resource-constrained SMEs. This financial accessibility enables smaller businesses to reap the benefits of automation without overextending their budgets.
Enabling Customization and Flexibility
In an era where customization is a growing demand, SMEs must maintain the flexibility to accommodate diverse client requirements. Traditional automation systems often struggle with small batch sizes and frequent changeovers, making them ill-suited for businesses that prioritize versatility.
Cobot automated welding shines in this context. Its programming is intuitive and can be adapted quickly to new tasks, allowing SMEs to switch between projects with minimal downtime. For example, an SME specializing in custom metalwork can use cobots to handle a wide range of welding tasks, from intricate artistic designs to industrial-grade components. This adaptability empowers businesses to pursue niche markets and respond to evolving customer needs without sacrificing productivity.
Improving Workplace Safety and Employee Satisfaction
Welding is inherently hazardous, involving high temperatures, bright light, and exposure to toxic fumes. By delegating repetitive or high-risk tasks to cobots, SMEs can significantly improve workplace safety. Cobots are equipped with advanced sensors that detect and respond to human presence, ensuring safe interactions and reducing the risk of accidents.
This shift also has a positive impact on employee satisfaction. Workers are relieved from monotonous or physically demanding tasks, allowing them to focus on using their experience to set up jobs and ensure quality. This can lead to increased job satisfaction, reduced turnover, and a more engaged workforce. By fostering a safer and more rewarding work environment, SMEs can enhance their reputation as employers of choice in a competitive labour market.
Case Studies and Real-World Impact
The adoption of automated welding using cobots among SMEs is already yielding tangible results across various industries. In the construction sector, SMEs have used cobots to accelerate the fabrication of structural components, reducing project timelines and costs. Similarly, small-scale manufacturers of agricultural equipment have leveraged cobots to enhance production efficiency while maintaining the durability and precision required in their products.
One notable example is a mid-sized metal fabrication company that integrated cobot welding to handle the production of steel frames for the renewable energy sector. By automating repetitive welds, the company reduced labour costs by 25% and increased production capacity by 40%. This allowed the business to expand its client base and compete with larger players in the industry.
Challenges and Future Prospects
While the benefits of cobot welding are compelling, SMEs may face challenges during implementation, such as the initial learning curve associated with programming and the need for ongoing maintenance. However, as cobot technology continues to evolve, these barriers are small and likely to diminish. Manufacturers are investing in user-friendly interfaces and robust support networks to ensure seamless adoption.
Looking ahead, advancements in artificial intelligence and machine learning are poised to further enhance the capabilities of cobot welding. Adaptive programming, real-time error detection, and predictive maintenance will make cobots even more reliable and versatile, solidifying their role as indispensable tools for SMEs.
Conclusion
Cobot automated welding is fundamentally reshaping the way fabrication SMEs operate. By addressing labour shortages, enhancing productivity, reducing costs, and enabling customization, cobots empower smaller businesses to compete on a larger scale. Beyond operational benefits, the technology promotes workplace safety and job satisfaction, creating a more sustainable and attractive industry. As cobot adoption accelerates, SMEs that embrace this innovation will be well-positioned to thrive in an increasingly competitive and dynamic market.
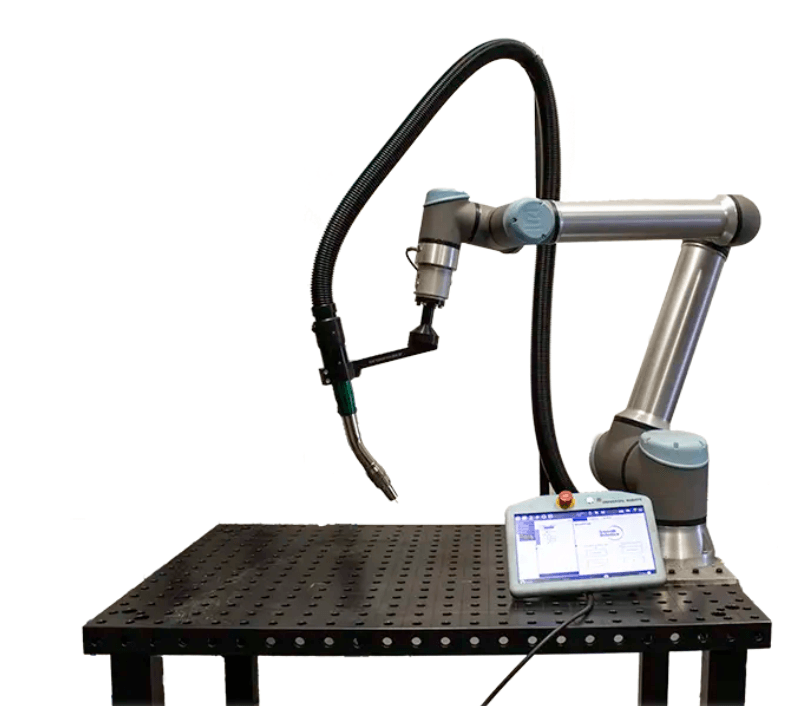
This article by Universal Robots is a great read to further your knowledge
Related posts
Fundamentals of MIG Welding Aluminium with a Cobot
Metal Inert Gas (MIG) welding is one of the most versatile and widely used welding methods. When it
Understanding Pulse MIG Welding: An Innovative Welding Technique
Pulse Metal Inert Gas (MIG) welding is a cutting-edge welding process that offers significant advant
How Cobot Welding Can Propel Your Business Forward
Understanding Cobot Welding Cobot welding significantly simplifies the welding process compared to t