What are the challenges in using cobot welding within your business?
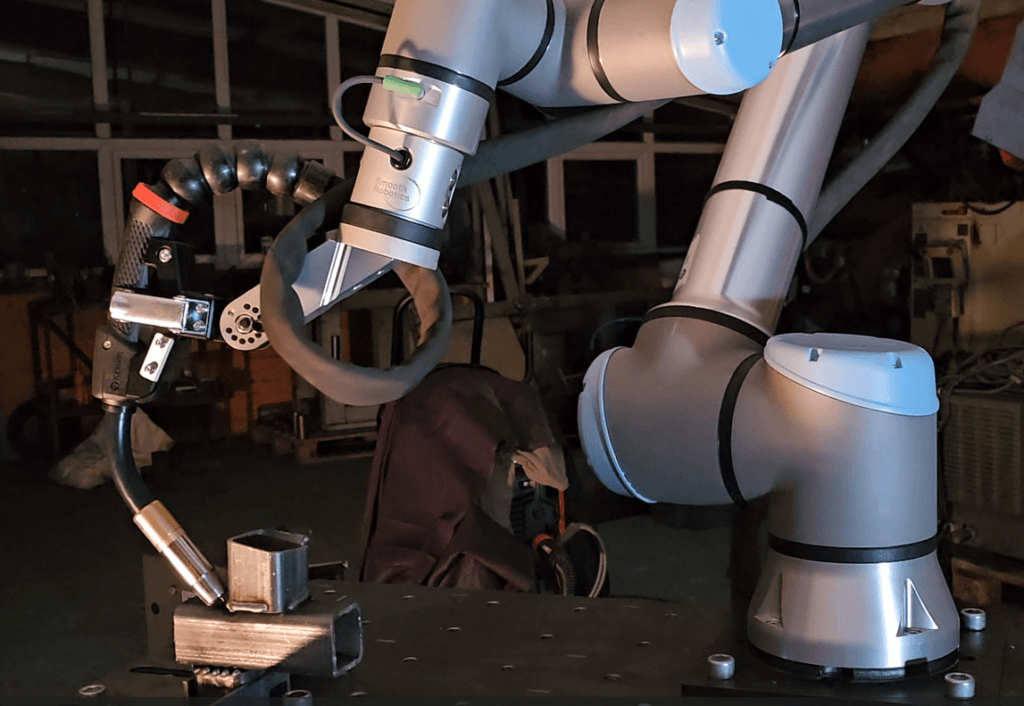
Implementing automated cobot MIG (Metal Inert Gas) welding, or
any cobot welding for that matter, in a manufacturing business can offer
numerous benefits, such as increased efficiency, consistency in weld quality,
and reduced labor costs. See our article, “How
can Cobot Welding Drive my Business Forward?” For more detail.” However,
there are also several perceived challenges associated with integrating cobots
(collaborative robots) onto a shop floor. These challenges can be broadly
categorized into technical, operational, and organizational aspects and are
discussed in more detail below:
1. Technical Challenges
1.1 Installing the system
There are two main parts to a cobot welding system; the MIG welding set (power source) and the cobot. There can be a number of challenges in terms of communication and safety depending on the equipment used and its age. At A3L we offer Kemppi welding sets, along with the Universal Robot, cobot, as these together offer an excellent welding solution and are extremely easy to install, setup, run and maintain. The two systems talk directly to each other using an interface communication module (DMC) and can be very quickly assembled with very little difficulty. There are other methods of communication the main one being general I/O but this is frequently more limited and with older power sources there may be no way to trigger the weld or carry out other basic communications. In this case a means of pulling the weld torch trigger or, by-passing it, would be necessary to weld, along with initiating gas flow etc.
1.2 Parameter setting
Once the cobot is setup and ready to go, parameters need to be set on the welder and then welding initiated, This can be challenging as most welding sets can only be manually set to one set of parameters at a time. This means that you can only complete welds with a single set of parameters before a manual intervention is required to adjust the parameters. Different welds need different parameters depending on many things such as weld direction, material, tickness, type,…. The Kemppi Master M has 100 programmable channels for MIG (it’s less for TIG and MMA) which can be automatically selected by the cobot. This means that different welds can be completed without intervention. Without the ability to switch weld settings automatically the cobot will be restricted in the welds it can complete, which may, or may not, be a problem depending on your needs.
1.3 Environmental factors
Welding processes generate a lot of heat, fumes, and spatter, making the environment harsh and dirty. Universal cobots are designed to work in industrial environments but we advise that precautions are taken to stop the ingress of dirt and damage from spatter. We supply protective coverings and design the systems to limit the exposure of the cobot especially the controller and teach pendant. Cobots, no matter the brand, are precise instruments and need to be protected where possible and handled with care.
1.4 Compatibility with existing equipment
Many manufacturing firms have existing welding equipment and infrastructure that may be older and not as compatible with cobots as the latest units. Ensuring seamless integration with existing systems, such as power sources and weld controllers, can be a technical hurdle. You can connect most power sources to a cobot but this can sometimes be at a cost to functionality, especially if the power source lacks key communication ability.
1.5 Material fit-up
Cobot welders will only do what they are told (programmed) to do which means that the part fit needs to be consistent and reasonably accurate. If your parts have wildly varying gaps and poor fit your weld will most likely show varying quality and possibly fail quality checks. With the use of laser cutting and good fixturing, this generally isn’t a problem, but poor consistency needs to be kept to a minimum.
2. Operational Challenges
2.1 Programming and job setup
Setting up and programming robots for welding tasks used to be very time-consuming and require specialized knowledge. Operators needed to be trained in programming and operating robots, which can be a significant learning curve. With cobots it is very simple. A3L offer Smooth Robotic’s programming interface which allows a welder with no robotic experience to pick up the programming process in only a few hours or less. This turns the cobot welding system into a welding tool for your existing welders, leveraging their knowledge in terms of how to complete a weld, set weld parameters and the ways to weld but letting the robot do the lesser skilled tasks like moving the weld torch along the weld path.
2.2 Changeover time
In a dynamic fabrication environment where product specifications and production runs change frequently the time required to program a cobot is significant. With Smooth Robotics software programming can be completed in seconds, if multipass welds are required only one weld needs to be taught again reducing massively the overall time requirement. The welder simply manually moves the robot arm to the start and end point of the weld and then presses go. Its that’s simple
3. Organizational Challenges
3.1 Workforce resistance
Employees may resist the introduction of cobots due to concerns about job security, changes in work routines, or fear of the unknown. We at A3L have found the best way to overcome this is to let your employees see and use a cobot welder, they soon realize it’s an efficiency tool and not a replacement for a person. Talk to us, if you would like us to bring a system to your site for a demonstration.
3.2 Training and skill development
Smooth Robotics software is extremely easy to use and fast to pick up and this sits on top of Polyscope, the UR software which has also been designed to be extremely simple and easy to use. Traditionally the development of the skills required to program and teach robots was significant but, this has changed over the last few years. As with all computer skills younger people tend to pick them up faster but there are many older welders approaching retirement that are quite comfortable with cobot programming and use. In fact, it’s been said that cobots can extend the working age of welders as they can take some of the ‘heavy lifting’. Older welders can simply be used to over see the whole process. The cobots can weld, younger apprentices can setup and move materials while the older experienced person can over see the whole setup and ensure things are set correctly.
3.3 Cost and ROI
A3L’s basic robot package starts at about £55,000 and so there is a significant investment to be made, but with the shortage of welders both in the UK and globally driving labor costs higher, return on investment can be months rather than years and is likely to get better. It is also worth noting that once the investment is paid off the returns increase hugely. There may also be incentives in the form of grants or other rewards that could be used
3.4 Safety and compliance
While cobot’s are designed to work alongside humans safely, ensuring compliance with safety standards and regulations is important. A3L excel in designing and implementing safe systems that will ensure your shop floor remains a safe and productive environment. Cobot welding systems are becoming common place and there use often improves safety. As with all equipment of this nature a risk assessment should be completed specific to the application at hand.
4. Strategic and Logistical Challenges
4.1 Custom vs. standard solutions
Deciding whether to implement a custom cobot solution tailored to specific welding tasks or use a standard, ‘off-the-shelf’ solution can be important. Custom solutions may provide better integration and performance but can be more expensive and time-consuming to implement. Please contact us about your requirements and we’ll be happy to advise.
4.2 Workflow integration
Integrating cobots into your existing workflows without disrupting production can seem like a challenge but the reality is somewhat different. In the same way you could add a welding bench into your factory you can add a cobot welding system. With the right design and consideration there is no need for fencing or rigid fixturing. The cobot seamlessly sits alongside your existing welding stations and adds to the productivity and flexibility of your shop.
4.3 Scalability and flexibility
As production demands change, businesses need to ensure that their cobot systems can scale and adapt to new requirements. Cobots are extremely versatile and can be reconfigured or adapted to suit multiple new changes. This is more of an issue with robotic welding where generally you have fixed cells configured around high running parts.
5. Conclusion
Implementing Cobot MIG welding within a fabrication company involves navigating some technical, operational, and organizational challenges. While the benefits of increased automation and improved welding quality are significant, careful planning should be undertaken to ensure your cobot system will achieve the goals you desire.
Related posts
Fundamentals of MIG Welding Aluminium with a Cobot
Metal Inert Gas (MIG) welding is one of the most versatile and widely used welding methods. When it
Understanding Pulse MIG Welding: An Innovative Welding Technique
Pulse Metal Inert Gas (MIG) welding is a cutting-edge welding process that offers significant advant
Automated Welding with Cobots: Revolutionizing Fabrication for SMEs
In the fast-evolving world of manufacturing and fabrication, Small and Medium-sized Enterprises (SME