Understanding Pulse MIG Welding: An Innovative Welding Technique
Pulse Metal Inert Gas (MIG) welding is a cutting-edge welding process that offers significant advantages over conventional MIG welding. It is widely used in industries ranging from automotive to aerospace, where precision, efficiency, and quality are paramount. This article delves into the principles, benefits, and applications of pulse MIG welding, highlighting why it has become a preferred choice for many manufacturers.
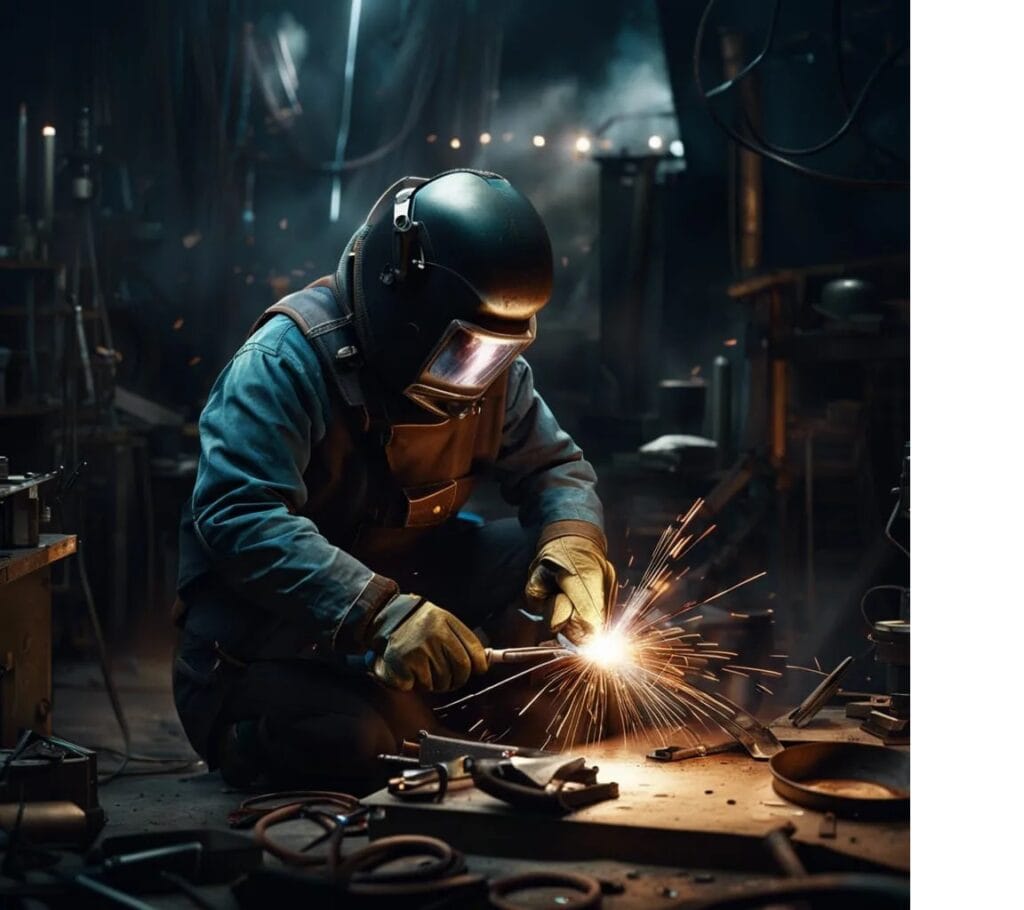
What is Pulse MIG Welding?
Pulse MIG welding is a variation of the traditional MIG welding process, utilizing a controlled pulsing of the welding current to enhance the welding arc. Unlike standard MIG welding, which uses a continuous and consistent current, pulse MIG welding alternates between a high current (peak current) and a low current (background current) in rapid cycles.
The peak current provides enough energy to melt the welding wire and create droplets, while the background current maintains the arc without excessive heat input. This controlled pulsing ensures that the welding process is more precise and adaptable to various materials and thicknesses. This video gives an excellent explanation in a little more detail.
How Pulse MIG Welding Works
The pulse MIG process relies on advanced power sources equipped with programmable settings. These settings allow welders to fine-tune parameters such as pulse frequency, peak current, and background current, tailoring the process to specific welding tasks.
As the current alternates, the arc produces a stable and concentrated heat zone. This results in reduced spatter, improved penetration control, and a cleaner weld bead. The technique is especially effective when working with thin materials or metals prone to heat distortion, such as aluminium and stainless steel.
Key Benefits of Pulse MIG Welding
- Reduced Heat Input
Pulse MIG welding minimizes heat input to the workpiece, reducing the risk of warping or damage to heat-sensitive materials. This is particularly advantageous when welding thin sheets or intricate components. - High-Quality Welds
The controlled pulsing creates uniform droplet transfer, leading to smooth and aesthetically pleasing welds. It also reduces spatter, minimizing post-weld cleanup. - Increased Efficiency
The process allows for higher travel speeds compared to traditional MIG welding. Welders can complete tasks more quickly without compromising quality, boosting productivity. - Versatility
Pulse MIG welding is suitable for a wide range of materials, including aluminum, stainless steel, and carbon steel. It can also handle various thicknesses with precision, making it a flexible choice for diverse applications. - Improved Operator Control
The technology offers greater control over the welding arc, enabling operators to adapt to challenging conditions or complex joint configurations with ease.
Conclusion
Pulse MIG welding is a transformative technology that combines precision, efficiency, and versatility. By leveraging controlled pulsing, this process addresses many challenges associated with traditional welding methods, offering cleaner, stronger, and more reliable welds. As industries continue to prioritize quality and efficiency, pulse MIG welding stands out as a vital tool in modern manufacturing. Contact us today to see a demonstration in your shop
Related posts
Fundamentals of MIG Welding Aluminium with a Cobot
Metal Inert Gas (MIG) welding is one of the most versatile and widely used welding methods. When it
Automated Welding with Cobots: Revolutionizing Fabrication for SMEs
In the fast-evolving world of manufacturing and fabrication, Small and Medium-sized Enterprises (SME
How Cobot Welding Can Propel Your Business Forward
Understanding Cobot Welding Cobot welding significantly simplifies the welding process compared to t