How Cobot Welding Can Propel Your Business Forward
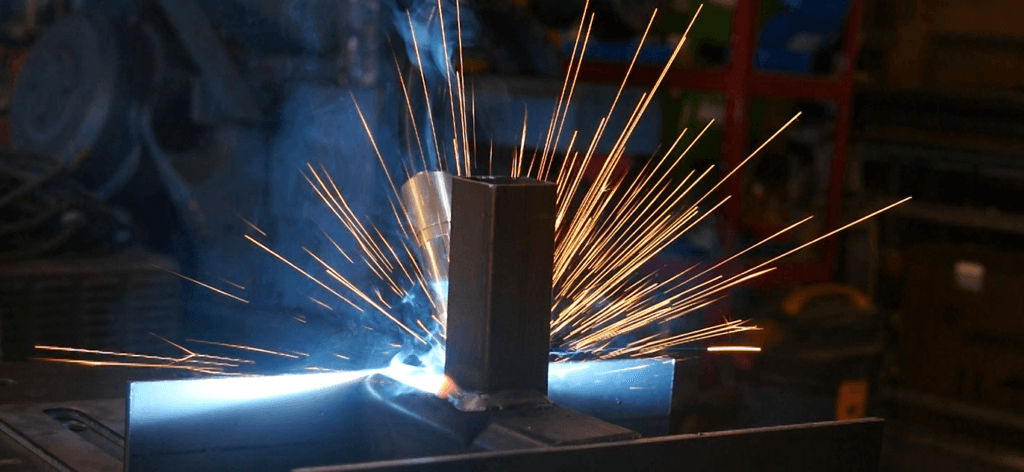
Understanding Cobot Welding
Cobot welding significantly simplifies the welding process compared to traditional robotic welding. With user-friendly programming capabilities, skilled welders can easily ensure optimal weld parameters for high-quality results. By simply guiding the cobot arm to designated start and end points, a straight-line weld can be set up in mere seconds. More intricate welds, which may require several more points, are also straightforward to program. The weld path can then be validated, making the cobot ready for operation in no time.
‘This efficiency allows your experienced welders to focus on other tasks while the cobot handles the welding.’
In essence, cobots serve as tools, efficiently maneuvering the welding torch along predetermined paths while relieving welders from this repetitive, monotonous task. Your seasoned welders will continue to ensure that appropriate welding parameters and procedures are followed, consistently delivering high-quality welds through the cobot.
Cost Efficiency
The cost of a cobot welding system varies based on application, with basic setups starting around £55,000, often yielding a return on investment (ROI) in under a year. As the demand for skilled welders increases and employment costs soar, cobots become a strategically cost-effective solution, enhancing both factory efficiency and production capacity. Additionally, the costs of these systems tend to decrease over time.
Swift Implementation
The implementation process is remarkably quick, with many companies up and running within hours of installation, including training. While mastering the equipment may take time, the basic operational understanding is accessible to all staff, regardless of their technical background.
One of the main challenges of learning new systems is maintaining momentum after initial training. However, the simplicity of cobot operation facilitates quick adaptation. Your welders will swiftly acquire the skills needed to carry out welds effectively and comprehend the equipment’s functionalities. Thanks to Smooth Robotics software, the learning curve is minimal, and A3L provides full support, although you may find it largely unnecessary.
Utilizing cobots can also enhance the speed of manufacturing. With their extended reach—often much longer than the manual repositioning required every 300mm—cobots can significantly reduce disruptions in welding runs. Moreover, the speed of the weld can be optimized with Kemppi’s latest pulse welding power sources, leading to greater efficiency and consistency across all welds.
Considerations for Success
To fully leverage the advantages of cobot welding, ensure that your chosen system accommodates all necessary requirements, such as fixturing and additional equipment. For instance, you may need a rotary device for certain components or a linear axis if you intend to operate multiple workstations with the same cobot. At A3L, we collaborate with you to ensure your investment meets all production needs with minimal expenditure on productivity and safety enhancements.
It’s also crucial to address workforce concerns regarding job security associated with automation—an issue commonly perceived in such transitions.
Conclusion
Cobot welding solutions provide a tangible way to address the global shortage of skilled welders. These systems can be seamlessly integrated into your welding team, akin to adding another manual welding station. Your team will quickly adopt new skills, resulting in immediate boosts in productivity. The initial fears regarding job loss will soon dissipate, as cobots become invaluable tools that empower your workforce and enhance productivity.
Contact us today for more information and an onsite demonstration
Related posts
Fundamentals of MIG Welding Aluminium with a Cobot
Metal Inert Gas (MIG) welding is one of the most versatile and widely used welding methods. When it
Understanding Pulse MIG Welding: An Innovative Welding Technique
Pulse Metal Inert Gas (MIG) welding is a cutting-edge welding process that offers significant advant
Automated Welding with Cobots: Revolutionizing Fabrication for SMEs
In the fast-evolving world of manufacturing and fabrication, Small and Medium-sized Enterprises (SME